TM 5-4220-231-14&P
3-30 Hydrocarbon
Inspection
and Analysis.
a.
Visual Method.
By definition, visibly clean
is the absence
of all particulate
and non-particulate
matter
visible to the normal
unaided
(except
for corrected
vision)
eye.
Particulate
is identified
as matter
of miniature
size
with observable
length,
width and thickness.
Non-particulate
is film matter
without
definite
dimension.
Examples
of visual
inspection
are:
(1) A clean
cloth placed
over the discharge
end may collect
particulates
and debris
when
air or nitrogen
is blown
through
the system.
(2) A component
that has
been
"in service"
may have visible
signs
of grease,
dirt, etc.
(3) Absorption
of oil or grease
on a clean
filter paper
from a surface
wipe.
b.
Ultraviolet
Light Method.
The ultraviolet
method
for detecting
hydrocarbons
may be employed
in several
different
ways.
WARNING
Most
ultraviolet
lamps
contain
mercury.
Extreme
caution
should
be taken
not to break
the
mercury
vapor
lamp which
will contaminate
the component
or pipe being
inspected
and may also cause
human
injury.
(1) Direct
Inspection:
The component
may be examined
directly with the ultraviolet
light.
By passing
the
component
under
the ultraviolet
light, hydrocarbon
surface
contamination
may
exhibit
fluorescence
where
some
hydrocarbons
exist.
(2) Inspection
of Cleaning
Solution
When
Detergent
is Used:
Used
cleaning
solution
collected
in a clean
beaker
when
agitated
will form bubbles.
These
bubbles,
under
ultraviolet
light, may exhibit
fluorescence.
3-31
Documentation
and
Record
Keeping
a.
This diving
system
must
retain
certain
records
and
documents
to substantiate
safety
standards.
The
individual
operating
the clean
area
being
directly
involved
with system
maintenance
should
therefore
be required
to maintain
records
documenting
cleaning
operations
in a systematic
manner.
b.
The
purpose
of this
section
is to set forth a guide
for documentation
and
record
keeping
involved
in
cleaning
operations
and
in no way intends
to impose
restrictions
on the amount
of paperwork
a unit feels
it requires
to operate
safely.
c.
A sequential
record
should
be maintained
of components
cleaned
(i.e.,
regulators,
pipe,
and/or
any
component)
affecting
reentry
into a certified
system.
It should
include
a written record
of all cleaning
analyses
and
testing
accomplished
as per this procedure.
A data
sheet
should
be completed
for items
cleaned
and tested
per
this procedure.
All other
information
which
pertains
to the cleaning
and/or
testing
of a particular
item shall
be
attached
to or referenced
on the
data
sheet.
Such
information
should
include,
but not be limited to outside
laboratory
reports,
vendor
data,
etc.
The completed
data
sheet(s)
will then
be attached
to the REC
Report
and
referenced
in the remarks
column
on the Reentry
Control
Log.
(Refer
to Para.
3-13).
3-48
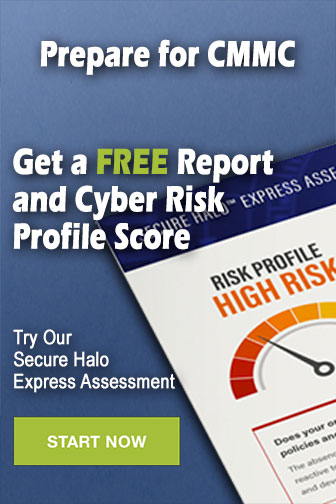