TM 5-4220-225-14
4-4. General. This section provides information and procedures for the receipt, installation, and testing of the MK12
SSDS.
4-5. Initial Inspection . Upon receiving the MK12 SSDS, all parts should be inspected and tested. The equipment may
not be ready for immediate operational use and some parts may require special preparation.
a.
Inventory. Upon receiving the equipment an inventory should be completed. To ensure receipt of all items, the
shipment should be compared with packing lists included in the shipping documentation.
b.
Inspection. Remove each item from the shipping container and perform a thorough inspection for any deviation
from good manufacturing and packaging processes, such as incompleteness of assembly, faulty. workmanship, rust, dirt,
delamination, cracks, deterioration, and corrosion. Specific items to be inspected are indicated in the following
subparagraphs.
(1) Helmet assembly. The helmet assembly of the MK12 SSDS is inspected to ensure all components are present and
in a condition suitable for use according to U.S. Army specifications.
(2) Dress assembly. Inspect the dress assembly, (drysuit, outer garments, boots, gloves, and weights) to ensure
components are present and in proper amounts. Ensure that all items are free from damage and
serviceable.
(3) Support equipment. Inspect support equipment to ensure that all components are present in proper amounts.
Ensure that all items are free from damage and serviceable. Support equipment consists of all items necessary for
diving operation's in excess of a fully assembled helmet and dress assemblies. Included are the following individual
items of equipment:
Umbilicals
Communication Cable Adapters
Test Set and Tools
Spare Parts Kit, Helmet Assembly
Repair Kit, Dress Assembly
Spare Parts Kit, Support Equipment
Shipping and Stowage Containers
c.
Maintenance Check. Examine maintenance records accompanying the shipment to verify that required preventive
maintenance checks and services have been performed. Perform all preventive maintenance checks and services as
scheduled before operational use of the equipment.
4-6. Operational Testing. Prior to operating the MK12 SSDS, it will be tested according to the procedures specified in
Chapter 2, Operating Instructions.
SECTION III. UNIT PREVENTIVE MAINTENANCE CHECKS AND SERVICES
4-7. Preventive Maintenance Checks and Services (PMCS). PMCS are covered in Chapter 2, Operating Instructions.
4-2
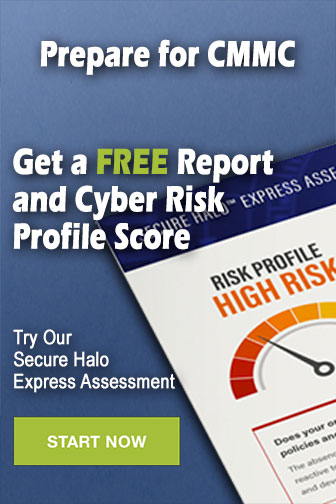