TM 5-4220-225-14
Table 2-1. Operator Preventive Maintenance Checks and Services (Cont).
Interval
Item
Item to be Inspected.
Equipment Will Be
No.
B
D
A
Q
Procedure
Reported Not Ready If
DRESS ASSEMBLY (Cont)
c.
Inspect the zipper for foreign matter, teeth align-
ment, and breaks in the zipper assembly tape.
d.
Visually inspect for dirt, grease, moisture, and
odor.
e.
If necessary, wash the suit with freshwater. Use a
Inspection reveals any of the
mild soap solution if required. Rinse with clean
defects sighted above or
freshwater.Allow the suit to dry thoroughly
any defect that renders the
before stowing.helmet inoperable.
16.
Leak Test.
CAUTION
Use only a MK12 helmet whose P setting is
known to be correct.
Leak test the drysuit in accordance with procedures
Drysuit fails test.
given in paragraph 2-8, d.
17.
Outer Garment Inspection.
a.
Inspect the suit for open seams, tears, abrasions,
dirt, grease, and odor.
b.
Inspect the Velcro closures to ensure they are
clean and in good operating condition.
c.
Check the weight pocket assemblies; calf, thigh,
and hip, for wear.
18.
Cleaning Procedures.
Wash thoroughly.Use a mild soap solution if
required. Rinse in clean freshwater. Allow to dry
thoroughly prior to stowage.
2-11
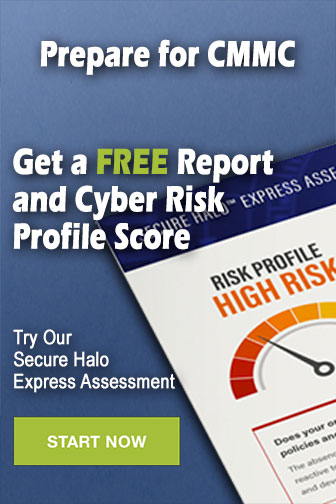